BLOG
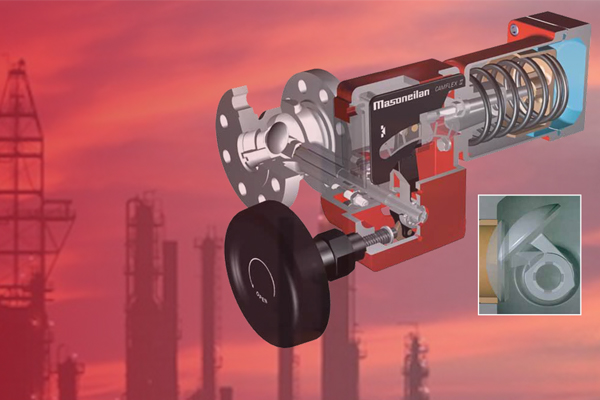
Masoneilan Camflex – Perfect design since ’69
- 15 May 2018
You may not realize it but Masoneilan is one of the oldest names in control valves in the industry. It is the combination of the Mason Steam Pump company from the late 1800s and the Neilan Regulator company, the two of which merged in 1931. For the next half of a century, they pioneered many innovations and established standards we still use today such as the flow coefficient calculations also known as Cv.
In 1968, ( ok so not since 69, but I needed a catchy title), they introduced the first Camflex. It was ground breaking then, and remains today, as a nearly perfect design for anything close to a “universal control valve”.
We all know there is no such thing as a universal control valve but the Camflex gets as close as any valve on the market. Let’s take a look at just some of the innovative features.
There is no better place to start than the cam and seat for which it get’s it’s name. Instead of a linear motion seating mechanism, the Camflex literally rotates on a splined shaft, with no friction across the seats, and flexes in to the sealing area. When released, it relaxes out and off the seat before rotating out of the flow path for a very trash tolerant, low friction design. This greatly reduced friction and wear improves the life of the valve and seat dramatically which leads to extend up time and of course, reduced unscheduled down time.
This design, commonly called an Eccentric Rotating Valve Plug, has been so successful, competitors have been watching the patents closely waiting for a chance to imitate it. Nothing satisfies customers more than reliability. In this area, the Camflex delivers and even better, it does so at a lower cost than comparable designs.
So how can they do it better and cheaper? As the title reflects, is is all in the design. It takes a lot less energy to rotate the splined shaft and lifting and lowering a linear piston. Because of that, the Camflex has few and smaller parts which also results in a much smaller footprint compared to Linear designs.
The design of the rolling diaphragm with a 3:1 force amplification and the piston action to control it insures a smooth 100:1 turn down for a smooth controlled flow from beginning to end. In addition, there is far less wear to the packing as it simple rotates within the packing instead of pulling media up and through the packing as linear designs due. This also allows the Camflex to be an Emissions Free design by default, not and extra costs add on as competitive products charge.
All of these unique innovations in the Camflex design result in a standard platform with amazing versatility. Through minimized friction, simplification in design and parts leads to increased reliability while optimizing control performance. When you combine this with eh amazing SVI II AP positioner, which deserves it’s own article on it’s innovations, there isn’t a better package available for most general applications.
Here is a more detailed list of features:
- Flangeless body rating is a rugged ANSI Class 600.
- Heavy duty guide lugs assure quick, positive alignment during installation.
- Flanged version available 1″through 12″(25mm through 300mm) in 150 or 300 ANSI and 1″through 8″(25mm through 200mm) in 600 ANSI.
- Separable Bonnet design available.
- Straight through flow pattern provides greater flow capacities.
- Standard integral extension bonnet allows for a wide range of fluid temperature applications(-320˚F to 750˚F), (-196˚C to 400˚C).
- The unique self-aligning eccentric rotating plug provides tight shut off and low dynamic forces.
- A large variety of reduced trim options are available in all sizes.
- The triple, over-sized bearing system provides exceptional plug shaft guiding.
- Shouldered shaft design.
- Optional patented differential velocity device (DVD) separates compressible flowstreams into a high velocity core and a low velocity envelope flowstream. Provides up to 18dBA noise attenuation.
- Optional alloy constructions are available.
- Powerful, low profile spring diaphragm actuator guarantees positive “fail-safe” action.
- Splined shaft and actuator linkages, combined with low friction techniques, assure minimum deadband and hysteresis.
- Large, highly visible valve position indicator.
- Totally enclosed actuator linkage (purge option available)
General Data:
Body
Type: cast with integral bonnet, cast with separable bonnet – 1″-8″
Flow Direction: flow to open or flow to close (Differential Velocity Device trim flow to open only)
Materials: carbon steel, 316 stainless steel (flangeless), 316L stainless steel (flanged), “Hastelloy C” (1″-4″) (DN 25-100)
Body Pressure Rating: ANSI Class 600 (per B16.34) standard (1″-12″) (DN 25-300) except for flanged construction; valve rating is limited by flange rating
End Connections:
- threaded- NPT for ANSI Class 600 rated connections (1″) (DN 25)
- flangeless- clamps between ANSI Class 150, 300 or 600 rated flanges (flange rating must be specified for 8″-12″(DN 200-300) valve for locator lug drilling and tapping)
- flanged- bolts to ANSI Class 150 or 300 rated flanges (1″-12″) (DN 25-300) ANSI Class 600 rated flanges (1″- 8″) (DN 25-200)
Trim
Plug Type: self-aligning eccentrically rotating
Materials:
- 1″-2″(DN 25-100) solid Stellite No. 6
- 3″-4″(DN 80 & 100) solid Stellite No. 6 optional
- 3″-12″(DN 80-300) 316L stainless steel with hardfaced seating surface
- 1″-4″(DN 25-100) “Hastelloy C”
- Seat Ring: solid clamped
Materials:
- 1″-12″(DN 25-300) 316 stainless steel
- 1″-4″(DN 25-100) “Hastelloy C”
- 3″-4″(DN 80 & 100) optional
- 1″-12″(DN 150-300) 316 stainless steel with hardfaced seat
- 1″-4″(DN 25-100) solid Stellite No. 6 optional
- 1″-12″(DN 25-300) 316 stainless steel with PTFE insert (to 450˚F), (232˚C)
Retainer: 316 Stainless Steel
Capacity: full area and reduced capacity in all sizes
Flow Characteristic:
- standard trim – linear
- low flow trim (.036 + .07 factor) – linear (requires SVI)
- differential velocity device – linear
CV Ratio:
- standard trim >100:1
- low flow trim 15:1
- differential velocity device >50:1
Actuators
Spring-Opposed Rolling Diaphragm
Size:
- 4½”diameter with 3½”(89mm) stroke (1″-2″valves), (DN 25-50)
- 6” diameter with 5¾”(146mm) stroke (3″-4″valves), (DN 80-100)
- 7″diameter with 7¼”(184mm) stroke (6″-12″valves), (DN 150-300)
- 9″diameter with 7¼”(184mm) stroke (6″-12″valves), (DN 150-300)
Range:
- 7-15 psi (1″-4″), (DN 25-100)
- 7-24 psi (6″-12″), (DN 150-300) (7″diameter actuator)
- 7-24 psi (6″-12″), (DN 150-300) (9″diameter actuator, Air to Close)
- 8-25 psi (6″-12″), (DN 150-300) (9″diameter actuator, Air to Open)
- Air Connection:1⁄4″NPT
Yoke: cast iron
Bearing: sealed radial
Auxiliary Handwheel:
- solid disk with locking nut
- 6 2⁄5″diameter (1″-4″valves), (DN 25-100)
- 10″diameter (6″-12″valves), (DN 150-300)
Manual Actuator
Type: solid disk with detent anti-rotation device. Continuously connected
Sizes:
- 7″(178mm) diameter (1″-2″valves), (DN 25-50)
- 8 7⁄8″(225mm) diameter (3″& 4″valves), (DN 80-100)
- 16 1⁄8″(410mm) diameter (6″-12″valves), (DN 150-300)
Material: aluminum
Yoke: cast iron
Bearing: sealed radial ball