BLOG
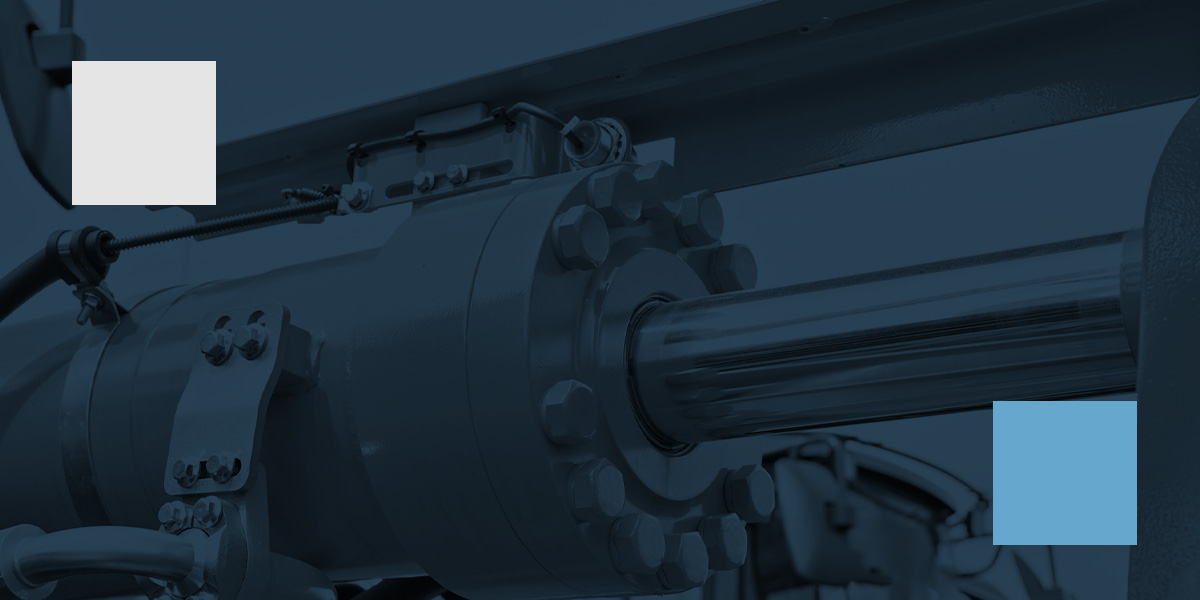
Common Control Valve Problems
- 10 Jul 2024
Control valves are used in a wide range of industrial applications. They regulate the flow of fluids, enabling systems to operate at peak efficiency. However, depending on the level of maintenance, control valves can wear over time. Knowing the common signs of defects is essential to reducing downtime and unexpected failures. This guide examines six top control valve problems and how to identify internal leakage in hydraulic systems.
Top Six Control Valve Issues
Proper care and regular maintenance can extend the life span of your control valves. However, you’ll likely start noticing some failures or defects over time. Some of these issues are common, including the following:
1. Internal Leaking Control Valve
Internal leakage is one of the most common but difficult-to-identify signs of defective control valves. Valves are designed with spaces, allowing an acceptable level of leakage. However, manufacturers cap the gaps at a maximum, and the leakage must stay within the prescribed limits. Once the leakage exceeds the limits, it causes multiple problems.
Hydraulic control valves may leak internally for many reasons. Common examples include incorrect calibration of positioners, improper setting up of actuators, and wear and tear of internal components. Another explanation could be that the distributed control system (DCS) is wrongly configured. A qualified technician can diagnose the problem, disassemble the valve, and replace the damaged parts.
2. External Leaking Control Valve
Control valves cause most external leaks in hydraulic systems. Leaking hydraulic fluid can damage the machine and pose health risks, but the good news is that external leaking is relatively easy to notice. Common causes include material incompatibility, faulty valve packing, and excessive component wear. Thermal cycling and vibration of the valve assembly can also cause external leaking.
3. Sticking Control Valve
Operators usually tighten the packing to stop leakages. The downside is that this can cause the valve to stick. Valves are designed with a specific packing torque value, and alteration could cause them to malfunction. Corrosion on the valve body or seat can also cause the control valve to stick.
A third explanation is debris contamination. In addition to causing the valve to stick, the accumulation of hard particles can cause leakages and other problems. To prevent this, it’s advisable to implement contamination control measures like planned maintenance schedules and filtration. A trained technician can disassemble the valve to clean or replace the affected parts.
Finally, positioner issues can cause stickiness, typical in pneumatic valves.
4. Change in Pressure in Hydraulic Control Valve
A change in pressure can affect the valve’s flow rates. This inconsistent flow may be due to clogged valve ports, incorrect sizing, or worn trim. To diagnose this problem, you can check the system’s dial indicator to assess whether the valve performs outside the expected parameters.
You may also want to check the positioning of the directional control valves to see if the fluid flow has stopped entirely. To fix the defect, technicians can disassemble and inspect the valve, clean or replace damaged components, and adjust the valve trim or sizing.
5. Noisy Control Valve
A noisy control valve is another common problem. Vibrations, turbulence, or cavitation could indicate that your control valve is faulty, so you should check for broken or worn parts. Adjusting the internals of the valve can also solve the problem. In some cases, installing noise-reducing devices is enough. It’s essential to address these issues immediately to prevent them from escalating.
6. Sudden Failure of Control Valve
Control valves could stop working when the components wear or deteriorate. This occurrence is usually expected, but you can reduce it with proper care and maintenance. Always use your machines for their intended purpose and ensure the actuator is the right size. Additionally, calibrate the positioners properly to prevent unusual breakdowns.
Choose control valves based on the size and process conditions, such as media, flow, and temperature. Using the correct components can extend the life span of your hydraulic machine and improve its efficiency.
How to Check if Hydraulic Cylinder Is Leaking Internally
Internal leakages could be challenging to detect. Fortunately, there are various techniques you can use to diagnose this problem. Here are a few examples:
- Visual Inspection: Sometimes, internal leakages manifest on the outside, and visual inspections can help. Check for oil stains or puddles on the cylinder body, piston rod, or nearby components.
- Operational Test: Operate the hydraulic systems and observe the cylinder’s performance. If you observe abnormal movements like jerking and drifting, there could be an internal defect. Also, listen for unusual noises like whistling and hissing, as they could indicate internal leaks.
- Pressure Drop Test: Perform a pressure drop test and monitor the gauge over time. A gradual pressure drop could indicate an internal leak.
- Fluid Analysis: Analyze the hydraulic fluid for any signs of contamination or air bubbles. Contaminated fluid can indicate internal leaks in the cylinder.
- Cylinder Rod Seal Inspection: Check the condition of the rod seals for signs of wear or damage. Damaged rod seals are the primary cause of internal leaks.
If you suspect an internal leak but are unsure how to proceed, consult a hydraulic systems specialist or technician for a more detailed inspection. They have the knowledge and resources to run an accurate and thorough diagnosis.
How Chalmers & Kubeck Can Help
C&K offers practical solutions to industries with control valve challenges. We provide a wide range of services, ensuring your hydraulic system performs optimally all year round. Below are some of the ways we can help:
- On-Site Testing: We provide on-site equipment inspection and testing to determine whether your system is functioning efficiently. Running diagnostics allows us to detect defects and propose efficient solutions to fix the problem.
- Repair: Our experienced technicians can repair and recondition the valves in your hydraulic systems. Our preventive maintenance solutions can reduce unexpected equipment malfunction.
- Replacement: We have an enormous inventory of replacement parts to fix various equipment. We can provide the ideal solution where original equipment manufacturer (OEM) parts are challenging to find.
- Training: We provide hands-on training to improve the technical abilities of technicians and supervisors. Our certified technical trainers are skilled in troubleshooting, disassembly, repairs, and replacements. We can tailor our programs to suit your training requirements.
Contact C&K for Efficient Control Valve Solutions
Control valves play a crucial role in hydraulic systems, maintaining proper fluid flow, controlling fluid temperature, and regulating pressure levels within the system. It’s vital to ensure the valves function optimally at all times, and C&K can help you achieve that goal.
C&K is a one-stop shop for industrial manufacturing, maintenance, and repair. Our team of factory-authorized and trained technicians is ready to assist. We also have a massive inventory to support various industrial needs. We take pride in everything we do and always strive to go the extra mile.
C&K has several accreditations and certifications that include ISO 9001:2015 and National Board Repair “R” and “VR” and we comply with the industry’s best practices and standards for quality service delivery. Want to learn more about our offerings? Contact us now!