BLOG
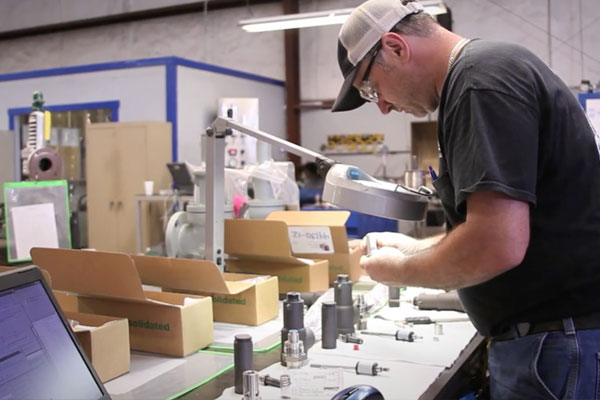
All Valve Service Shops are not Created Equal
- 18 Nov 2014
Not long ago, it was common for companies in the chemical, power and refining industries to have personnel on staff to handle many valve maintenance and service activities. But today, as skilled personnel of the Baby Boom generation retire and companies face increasing pressure to contain costs, a growing number of firms are turning to outside vendors to help care for their valves.
Careful consideration and a bit of homework are required in selecting this partner. This article will outline the criteria to consider.
Manufacturer-authorized Service Provider
Most valve manufacturers have a list of authorized service providers. You are certainly not required to choose one of these providers, but the credential is a sign of a quality shop.
To become an authorized service provider, a shop typically must meet criteria set by the original equipment manufacturer (OEM) in such areas as integrity, safety and environmental compliance, and the team must complete the manufacturer’s training program. In addition, manufacturers usually hold their certified shops to high standards when it comes to their facilities, equipment and staff expertise. Knowing that a service provider meets these criteria can give you added confidence that you are dealing with a reputable firm.
An authorized service provider also is likely audited regularly by the OEM. Yes, ISO 9000 is good, but it is not a valve operating guideline. When it comes to valve assembly/ testing and repair, the manufacturer is best equipped to conduct the detailed review necessary to ensure that the service shop is meeting the relevant standards. Reputable manufacturer-authorized service providers will be happy to show you their audit reports.
Additionally, OEM-authorized service providers have access to important details regarding the properties, construction and workings of a specific valve or part. Manufacturers build their products to meet unique and exacting specifications provided by the customer. Yes, a valve or part can be re-engineered, but only the OEM knows the original specs with certainty.
A manufacturer-authorized service provider receives extensive product training from the OEM and can consult with the manufacturer’s engineers to diagnose problems. An OEM-authorized shop also will use OEM parts, rather than re-engineered parts, helping ensure that the valve performs as expected.
Finally, not using a manufacturerauthorized service provider may invalidate the manufacturer’s warranty.
Asset Management Tools
The ability to provide asset management tools can be a significant differentiator between valve service shops. These tools put valve records – including repair data, repair records, test documentation, wiring diagrams, and “before” and “after” photos” – in a single, easily accessible database. You own the data and the link to it and can access the information 24/7.
This added capability can simplifyrecord-keeping for inspections and make it easier to meet reporting requirements. Asset management tools also provide diagnostic test reports and other data that can help you see performance trends over time, prepare for repair activities and manage your parts inventory.
Trained Technicians
When you were choosing your physician, among the factors you likely considered were his or her education, training and other credentials. The same criteria should apply when choosing a valve service partner. Ask to see the firm’s training certificates. Ask whether the technicians are trained in the latest OEM standards and relevant standards from such organizations as ASME (American Society of Mechanical Engineers). Also ask whether the technicians’ certificates are up-to-date; training is not a one-time task, but a continuous process.
Diagnostics Capability
When your car is making an odd noise, your mechanic frequently uses computer-based tools to diagnose the problem. A solid valve service provider will have similar tools in its arsenal. For pressure relief valves, the technician should have electronic valve testers that can test a valve in-line and in production (in-situ). For control and line valves, technicians should have a diagnostic unit that can compare current valve data to “Day One” baseline data. With a significant number of analog positioners still in use, these devices help remove the guesswork from assessing valve health.Access to InventoryEven the best technician cannot get your process running again without the necessary parts, replacement valves and other devices. Strong providers will have shelves wellstocked with OEM parts, valves, positioners, etc.
Certainly, it is impossible for a service provider to have every SKU in its warehouse. Affiliation with a network of service facilities can provide access to millions of dollars of inventory that can be on hand in days, and sometimes even hours. Ask a prospective service partner if it belongs to such a network.
Technological Expertise
A growing number of facilities are adopting such digital technologies as wireless communication, the HART® Protocol, the FOUNDATION™ fieldbus and PROFIBUS®. A strong service provider will have a “Digital Champion” who can guide you and who has the technical expertise and financial acumen to advise you on when to upgrade to digital technology.
The Facility
A tour of a prospective service partner’s facility can be telling. Learn about the firm’s capabilities in such areas as sandblasting, machining, welding and painting. Take note of whether the shop is neat, clean and well-lit. Organization is closely correlated to quality; after all, would you hire an accountant whose office is wall-to-wall stacks of paper?
As an added benefit, top providers also have onsite facilities where they offer training for their customers.
Choosing a valve service provider requires time and effort. But given the importance of valves to a facility’s performance, it is a decision that should not be taken lightly. Do your homework. It will be time well spent.